CAPABILITIES
3D Printing
D.W. Clark utilizes 3D printing to rapidly and cost effectively produce pattern tooling and direct printed molds. When people first hear, “3D printing,” their thoughts often go straight to the end-product with printed parts in metal and plastic. Depending on the needs of the project, we can print tooling over a weekend to be ready for a production run the following week. For prototypes and production runs of precision sand castings, we have two large format 3D mold printers that can have 3D printed molds ready for casting overnight, without any tooling required. Through our 3D mold printing casting process, neither of these applications require any changes to the casting material properties or specifications and we’re able to dramatically reduce the lead time, and often the cost, of a standard pattern tooling and casting process.
We use 3D mold printing casting for rapid prototype production and emergency shortages, and also employ 3D printed molds for precision sand casting to create better and more exact molds for casting. 3D printing technology can be used to lower tooling costs, provide ultra-fast delivery and achieve part geometries that cannot be made with traditional tooling.
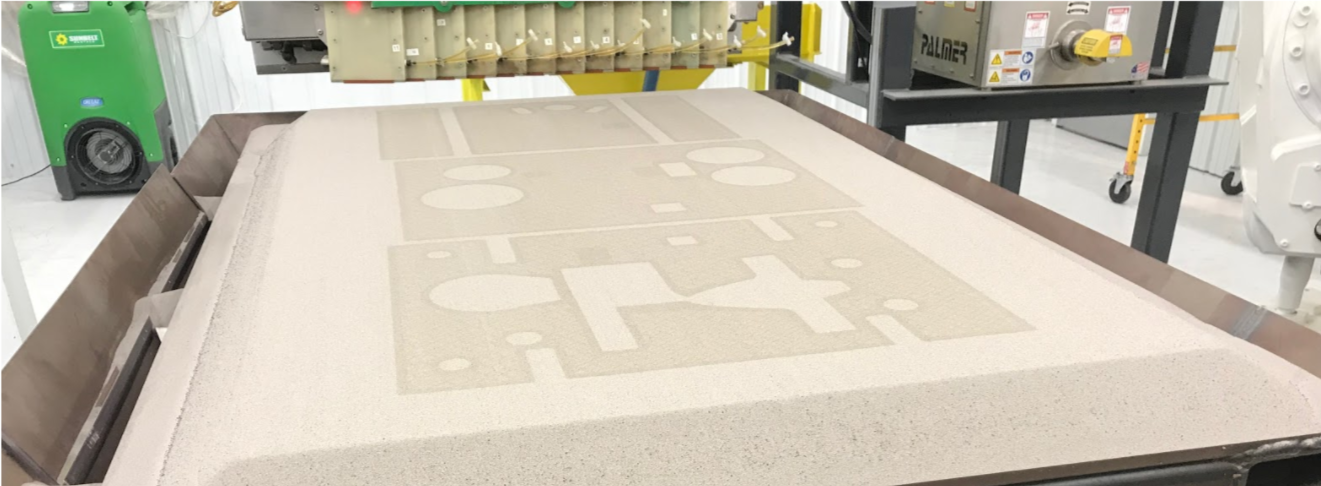
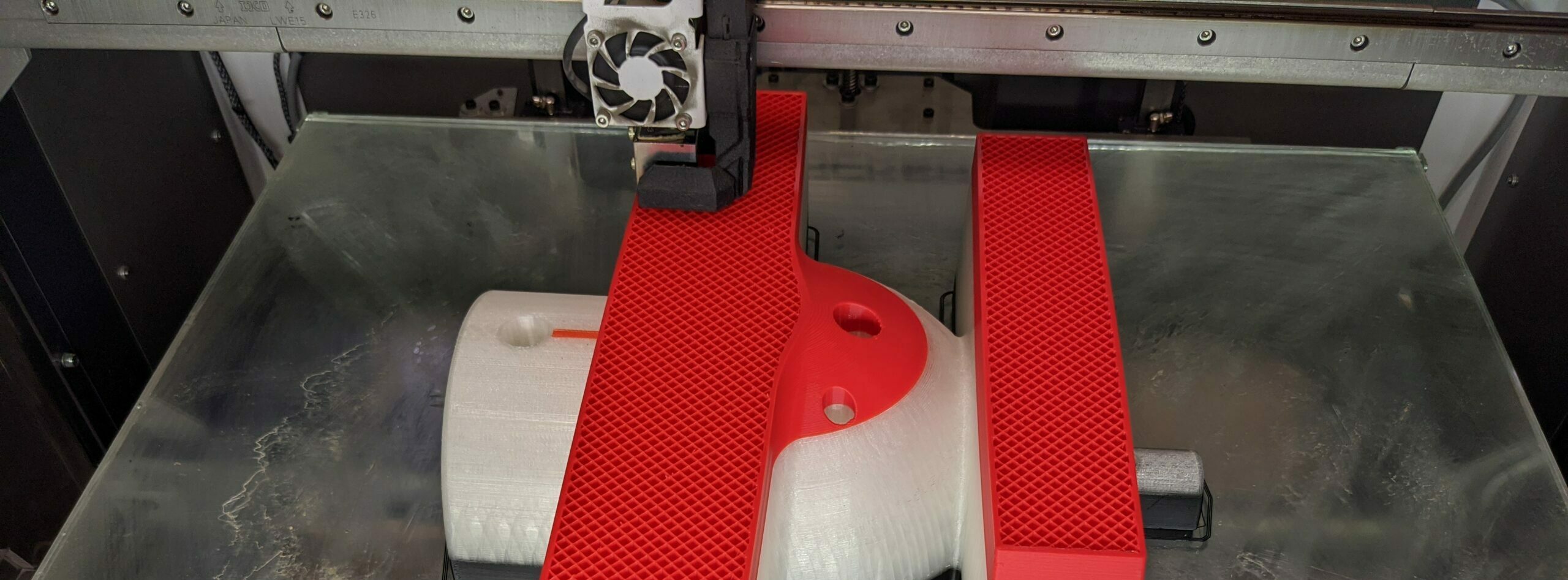
Rapid Prototyping
- For the development of new parts, or testing of existing part updates
- No geometry is too complex to be cast
- Low volume production ensures decreased prototyping production costs
- Additional cost savings and production efficiency as a result of multiple 3D printed molds that can be made quickly and at a lower cost than traditional tooling
Tooling
- For demanding applications that require specialized castings which are difficult to make
- Castings for the most complex of geometries, including re-engineering a part traditionally made of several parts into one whole mold
- Expedites new castings required as a result of emergency shortages, design updates or specification changes with the added benefit of cost savings
- Ensures high quality castings with tighter tolerances and better surface finishes, and uniformity of parts
How it Works
Mold Design
- Casting simulation/methods
- Derive mold from gating and riser layout
- Adjust mold as needed for manufacturability
- Start with a 3D CAD file of the part
- Import 3D model files into printer software
- Arrange 3D molds and cores within the printer build envelope
- Run printer
Post Process
- Remove build box from printer
- Remove loose sand from molds and cores
- Clean molds and cores to be free of any boundary-layer sand
Prep and Assembly
- Prepare molds with any coating or layout features
- Assemble and close molds/core
Non-Destructive Testing
Non-Destructive Testing (NDT) is a critical part of the process for many parts and applications. D.W. Clark has an extensive depth of experience with NDT for defense, aerospace, turbine engine and marine systems applications. Thousands of castings are produced each year that meet commercial and military NDT requirements including ASTM, ASME, AMS and NAVSEA Tech Pubs.
RT – X-Ray Radiography Testing
X-Ray is regularly used for qualifying first article castings and on production runs for critical applications. It is used to identify and characterize the level of internal soundness for a part.
PT – Liquid Penetrant Testing
Utilizing a fluorescent or visible dye with full or partial coverage over a part that is then removed and developed, PT is a cost effective non-destructive testing method for detecting surface-breaking discontinuities.
MT – Magnetic Particle Testing
By applying magnetic particles to a part, as a powder or in a liquid suspension, and applying magnetic current, surface and subsurface discontinuities are detected on ferromagnetic alloys.
UT – Ultrasonic Testing
Using ultrasonics, subsurface discontinuities are detected and wall thicknesses can also be measured.
VT – Visual Testing
With trained and certified inspectors, visual testing is used to inspect and qualify casting surfaces to recognized standards.
Machining
D.W. Clark offers extensive machining capabilities, with a substantial and increasing number of the sand and centrifugal castings we manufacture being provided to customers with finish machining. This gives our customers the option to streamline their supply chain, focusing on completed parts and relying on D.W. Clark to deliver finished castings with all of the requirements met. We often have a strong understanding and experience with the finish machining needs of both the sand and centrifugal castings we produce, and can leverage this to provide our customers with the best overall solution.
Rough Machining
- For bringing a part close to finish, qualifying and preparing a part for finish machining
- All centrifugal castings and many of our sand castings are or can be provided semi/rough machined
- Offers material cost savings and improved quality
Finish Machining
- Providing parts complete to print
- Often parts have additional testing requirements after finishing, such as NDT, that can be provided complete
- If it is beyond our machining capability, we have deep experience and relationships with sources who can finish just about every casting we make
Integrated Services
D.W. Clark provides our customers with complete solutions to meet their needs. In addition to our core value-added services, we offer a range of capabilities to take your part further by simplifying the sourcing process. Between our in-house capabilities and network of processing relationships, we can be your single source for a completed part.
Additional services we provide include:
Hydro testing
Assembly and fabrication
RT Radiographic Testing (X-ray)
PT Penetrant Testing
MT Magnetic Particle Testing
UT Ultrasonic Testing
Heat Treatment
Welding
Sandblasting
Painting
Passivating
VT Visual Testing